MECSPE fair in Bologna ended and we are truly grateful to all those who came out to see us.
It gave us the opportunity to display a selection of our measuring instruments and to discuss various measuring needs in person, without technological barriers.
This is the aspect we like most, meeting our loyal customers directly and creating new ones.
We listen to what the company produces, what results it would like to achieve, or what problems need to be resolved.
SAMA Tools name-brand measuring instruments were created to cater these needs, but we also think that the assistance our technicians are able to provide pre-purchase can really make the difference.
What animates our company are certainly the people who, if you came to the fair, you will have met, albeit partially, because others remained at our headquarters in Viareggio.
Measuring instruments at MECSPE
For the 2023 edition of MECSPE, we selected various types of tools, suitable to satisfy the needs of manufacturing companies in various sectors.
Automotive, Oil & Gas, Naval, Food, Industrial Painting, Molds etc.
Force Measure
The measure of force encloses all tests essential for the quality and resistance of a specific product.
The main force tests include:
traction,
compression,
torque.
These measuring instruments can be found in the section “Force measure”.
Measuring of the hardness of materials
When measuring the hardness of materials, we rely on portable or bench hardness testers.
There are different types of portable hardness testers, depending on the type of material or test to be carried out. They are mainly used to assess the hardness of the material for quality control in the production line and for the maintenance of structures and parts which are subject to wear.
These measuring instruments can be found in the section “Measuring the hardness of materials”.
Ultrasonic thickness measurement
To measure the thickness of a specific piece, the ultrasound technique is particularly recommended, as it allows you to measure a detail by simply placing the probe on it, without the need of any feedback from the opposite side.
In this case, the measuring instruments are the thickness gauges, which determine the thickness of a material by accurately calculating the time required by an ultrasonic pulse generated by the probe to pass through the thickness of the sample, which is reflected on the opposite surface and then returned to the probe.
Ultrasonic thickness gauges are ideal in the production phase, quality control, input control, PED inspections, material approval, output control and in all non-destructive tests where it is not possible to access both sides of measurement.
New Product! Fiberglass thickness gauge
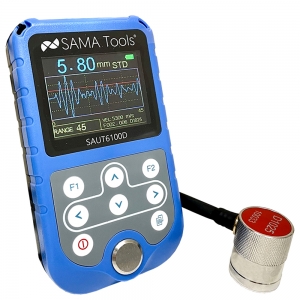
In the photo: Fiberglass ultrasonic thickness gauge – SAUT6100D-SW
This new model, as seen in the photo, was first presented at MECSPE. It is a graphic ultrasonic thickness gauge for fiberglass and composite materials. If you were present at one of our demonstrations at the fair, you will have seen how easy it is to use and its great potential for various fields, like boating, automotive, Oil & Gas, etc.
To verify that this tool is suitable for every specific need, S.A.M.A. can carry out tests directly on samples provided by our customers or alternatively, our technicians can personally go to shipyards or other establishments and carry out tests on site. Other thickness gauges can be found in the sections:
Ultrasonic thickness measurement

In the photo: Rotational abrasion tester – SAAB523
Another highly appreciated measuring instrument was the Rotational abrasion tester, mainly used to determine the abrasion resistance performance of various coatings by rotational rubbing, or to determine the abrasion resistance of paper, plastic, fabric, decorations, etc.
The samples are placed on the rotary plate and then subjected to the action of abrasion by two abrasive wheels with a determined pressure. The abrasive action is obtained by rotating the sample, while two abrasive wheels rotate above it. The wheels complete a full turn on the surface of the sample which allows to check the abrasion resistance at all possible angles of that sample.

In the photo: Digital rotational viscometers – SAVISC152
The Digital rotational viscometer is ideal for testing the viscosity and resistance of a fluid.
The elegant model in the photo constantly controls the rotation speed and is widely utilized in chemical, medical, food, industrial, laboratory, scientific research fields, etc.
When an operator has to carry out the viscosity measurement in the laboratory, it is not always easy to identify the most suitable viscometer model. In these cases, our technicians are available to listen to each specific need and indicate the most appropriate solution.
This pre-sale consultancy service is free and allows us not only to concretely help our customers, but also to significantly reduce returns due to incorrect orders. Our philosophy is to always implement all preventive actions to avoid buying the wrong instrument.
Mechanical measuring instruments
The measuring instruments in our mechanical section are never lacking at the fairs we attend, since their use is extremely important and common in all manufacturing companies.

In photo: SAMA Tools micrometers and calipers
Mechanical measuring instruments can be found in the “Mechanical section”
Calibration of measuring instruments
At MECSPE, we also talked about our calibration services. Measuring and control instruments play a very important role within the production process of a company, such as guaranteeing the suitability of manufacturing products.
It is necessary that the instruments are efficient and remain within the tolerance range as dictated by the piece. It is therefore essential to calibrate all instruments, even the simplest ones.
In this regard there are often many uncertainties, and our customers ask us questions like these:
- What does ISO 9001 say in detail regarding calibration?
- Why is it important to calibrate measuring instruments?
- When should the calibration be repeated?
- How long should the instrument be used before it is subjected to calibration and certification?
- What if the certification does not go well or has errors?
- What if the measuring instrument cannot be certified?
- Do I need a calibration report or Accredia certificate?
- What are the differences between calibration and Accredia certificates?
If you also have these kinds of questions, firstly, we recommend that you subscribe to our newsletter because in addition to providing you with useful information on the various types of measurements, it allows you to immediately receive an ebook on the ABCs of calibration via email.
Instrument calibration is necessary and useful for many industrial sectors. Likewise, it is essential to have a solid intervention program to ensure minimal downtime.
S.A.M.A. Italia is ISO 9001 certified to provide calibration reports and collaborates with the best accredited centers for LAT / Accredia certificates.
If you want more details of the 3-day fair, follow us on Instagram. You will find photos and mini-videos of our name-brand SAMA Tools measuring instruments.