Today, Ecol Studio Spa is a well-known company that works in various areas including health and safety in the workplace, but this company also does much more. Let’s read on to find out more.
All our customers have different stories. Some are described on their websites; others are found in books. This is the case of Ecol Studio Spa and through its founding member, we are able to read the pages related to its history, which is chalk-full of events and difficulties which were faced and eventually overcome.
The origins
Back in 1982, Guido Fornari and his two friends, founded Ecol Studio, located in Garfagnana, Lucca, in the splendid region of Tuscany.
It was a very small company that worked in environmental analysis.
Initially, the income generated was not enough to meet the needs of three families, and eventually the three friends parted ways.
Guido pressed on, also working in another company to make ends meet, but without ever losing sight of his biggest goal: to make a billion lire in 10 years!
The dream began to take shape five years later, when Ecol Studio expanded, making use of trained staff such as Mario Santi, an employee who became a very important technical figure for the company.
From that moment on, the company has grown exponentially, both in the number of collaborators, offices opened in the area and of course, in turnover, which exceeded the initial target even before the hoped for 10 year mark.
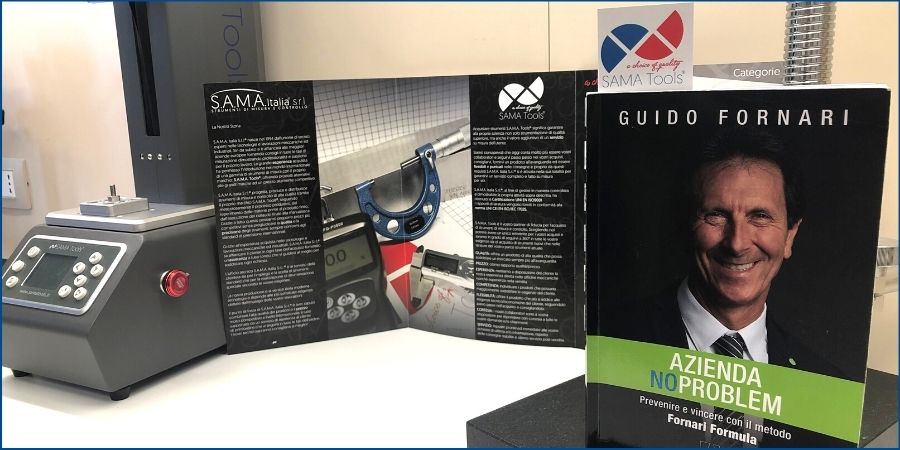
In photo: the book by Guido Fornari with SAMA Tools material
Ecol Studio today, not only health and safety
Today Ecol Studio assists the growth of companies to implement policies aimed at sustainable development.
The analysis laboratories are ACCREDIA certified, in compliance with the UNI CEI EN ISO / IEC 17025: 2018 reference standard.
The main operational areas of the company are:
Health and safety with regularly calibrated measuring instruments
Ecol Studio has always promoted prevention in the workplace, to avoid accidents and occupational diseases and ensure the physical, mental and social well-being of each worker.
It assists companies in compliance with the laws, to avoid sanctions and implement organizational and management models.
The company prepares the DVR, the risk assessment document in relation to the production activity carried out and the dangers present. In addition, Ecol carries out all the necessary measurements, with high-performance and regularly calibrated measuring instruments.
Examples of measurements include:
- Ergonomics and manual and mechanical use
- Noise, vibrations, electromagnetic fields, optical radiation
- Confined environments
- Microclimate
- Electrical risk etc.
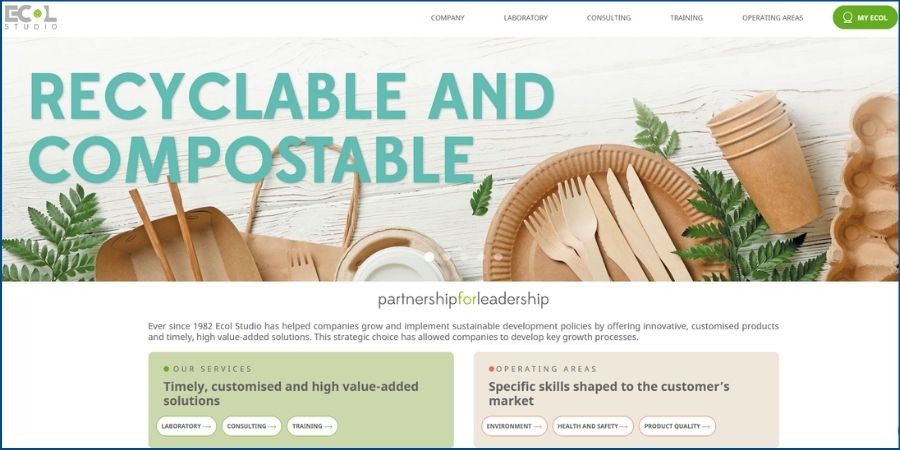
In photo: some of the application fields of Ecol Studio
Environment
Ecol Studio also aims to assist companies with compliance concerning environmental regulations and to improve their green and energy performance.
These are always very delicate processes that require monitoring, compliance with delivery times and the presentation of practices.
Ecol manages everything by collaborating with the relevant bodies.
Product quality
Ecol Studio offers reliable solutions and tests to create products and implement processes that comply with the required standards, following the constantly evolving current legislation.
The generational transition of Ecol Studio
In 2021 Guido Fornari published the book entitled: “Da un sogno a multinazionale” where he writes about how he managed the generational transition of the company, by allowing his two sons to work in the company. One of his two sons, Claudio Fornari, “ate, breathed and slept” the company as a child and also had important experiences outside the family business; he was then able to reinterpret his path in an original way, gradually assisting his father at the helm of the company.
Over the years, the other son expressed a desire to create a different business and left the company.
It is a good story to read about and reflect on. It also sends a very clear message: “Children can be a great opportunity for a family business, just as the company represents a great opportunity for them. However, there must be no obligation, no pressure, no ones destiny is already written.”
In 2021, Ecol Studio S.p.A. also joined the Lifeanalytics group, contributing to the development of the largest network of laboratories in Italy at the service of companies.
“The more we are, the better we make the world! … In the last forty years, teamwork has allowed us to achieve extraordinary results together, along with our customers … Today, the same vision and the same culture allow us to take a step forward: the partnership between Lifeanalytics and Ecol Studio represents a strategic union of companies” Cit. Guido Fornari

In photo: the history steps of of Ecol Studio
Ecol Studio collaborates with S.A.M.A. Italia to keep their measuring instruments always calibrated.
Guido Fornari, in his book: “Azienda no problem” of 2019, affirms the importance of choosing strategic partners, which allows you to conduct your business in the best and most proficient way possible.
“When it comes to professionals, surround yourself with the best if you want great performance. It is useless to save by relying on someone with little experience … It is your responsibility to choose the best partners”
Based on these premises, Ecol Studio has chosen S.A.M.A. Italia as a strategic partner for the purchase and calibration of measuring instruments since 2014.
The calibration and maintenance of Ecol instruments are performed in accordance with the reference technical standards and the recommendations of the control body (Accredia accredited tests).
SAMA Tools measuring instruments
The business areas in which S.A.M.A. Italia operates are many, including the monitoring, testing and control for the measurement of Temperature, Pressure, Relative Humidity, Air Quality, CO and CO2, Microclimate, Photo-radiometry, Air Speed, Acoustics and Vibrations.
The brand we recommend, in addition to our own SAMA Tools brand-name instruments, is Delta Ohm, an Italian company specialized in the parameters described above, of which we are authorized resellers in many regions of Italy.
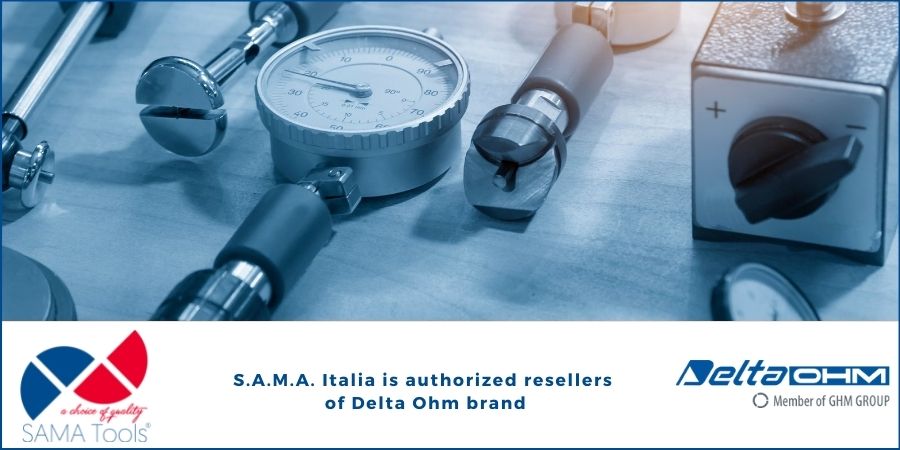
Photo by www.canva.com: SAMA Tools and Delta Ohm
Measuring instruments calibration service
In addition to measuring instruments, we also offer calibration services on other brands of instruments.
We are talking about both standard calibration reports with reference to acknowledged samples which we directly supply, and ACCREDIA certificates.
We are very careful to select accredited calibration centers with modern laboratories equipped with state-of-the-art equipment.
Delta Ohm is accredited for physical quantities, such as Temperature, Humidity, Pressure, Air Velocity, Acoustics, Photo radiometry. Therefore, we are able to provide our customers with complete kits of instruments with subsequent periodic calibrations.
Our mission
Our mission is to assist customers in their quality control activities, and we are committed to providing the best solutions to meet their individual needs, as in the case of Ecol Studio Spa.
Do you need help with measuring tools to ensure high accuracy and high quality? Are you looking for advice on the best instrument for your specific needs? Don’t hesitate to contact our technical department!
Call us at 0584392342 – 0584392453 or write us at sales@samatools.it